POLYVINYL ALCOHOL
POLYVINYL ALCOHOL FOR INK JET PRINTING PAPERS
Advances in ink jet printing technology have resulted in a new generation of ink jet printers which can print faster at wider paper widths, producing four-color images close to photography quality. Ink jet printing papers must respond to these changes through quick ink absorption, minimizing ink bleed and ink wicking while retaining favorable ink optical density values. To meet these demands, many papermakers are turning to pigmented size press and coatings formulations. The pigments of choice for ink jet formulations are typically precipitated, fumed or colloidal silicas, and the binder of choice is Selvol Polyvinyl Alcohol (PVOH) because of this material’s unique performance characteristics.
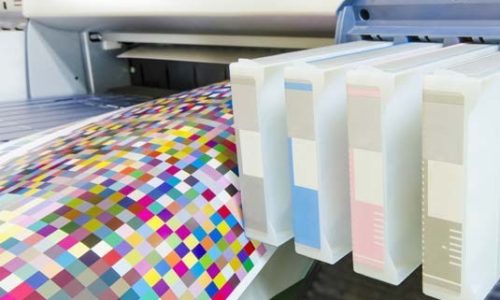
Ink jet printing papers are generally size press or surface coated with formulations that include structured silica pigments. These pigments have large surface areas in the range of 50 to 700 m2/gram. They are highly absorptive and thus, possess a substantial binder demand. Typical pigment binders used in size press coating formulations, such as starch or latex, are either weak in their binding strength, therefore creating a dusting problem, or they interfere with ink absorption during printing, resulting in poor ink jet printing quality.
The performance benefits of Selvol PVOH for pigmented ink jet papers relate to the material’s excellent binding strength, affinity for water and, in some cases, its ability to boost optical brightener performance in high-brightness ink jet papers. PVOH can be used successfully as a binder at the size press in lightly pigmented formulations or as a binder in coatings where silica pigmentation levels are much greater.
PVOH FOR PIGMENTED INK JET SIZE PRESS AND COATING APPLICATIONS
In ink jet coatings, the molecular weight of PVOH controls the binding power for pigment adhesion and also determines coating rheology. The percent hydrolysis also helps control the binding power and coatings rheology, but to a lesser extent than a molecular weight. Table 1 illustrates the grades of Selvol PVOH that are commercially available.
The recommended Selvol PVOH grades for size press applications of silica pigmented formulations are Selvol 107 and Selvol 325. These grades are fully hydrolyzed (98.0 to 98.8% hydrolysis) at low and medium molecular weights respectively. Selvol 107 and Selvol 325 PVOH grades both offer excellent binding strength for the silica pigment, and they provide good monochrome and color optical density as compared with conventional size press starch. Ink dry times are reduced with the addition of the silica in comparison with straight PVOH. The following information highlights these attributes.
BINDING POWER
PVOH is widely recognized as the strongest binder available in the paper industry and, according to TAPPI Monograph No. 37, is 3 to 4 times as strong as starch, depending on the PVOH molecular weight. Its use permits significantly reduced binder levels in size press formulation and maximum utilization of the silica’s high absorption capabilities without dusting or linting problems, as seen in Figure 1. The strength of PVOH also allows for offset printing without silica linting or dusting prior to ink jet printing, when that sequence of printing is necessary
SIZING AND OPTICAL DENSITY
The extent to which a paper is internally sized, or the combination of its internal and surface sizing, may have a significant impact on print optical density. In a slack-sized base sheet, Selvol PVOH can provide a boost to black and composite black optical print density compared with starch. Specifically, fully hydrolyzed PVOH, such as Selvol 107 (low molecular weight) and Selvol 325 (medium molecular weight), yields excellent monochrome black and composite black optical densities, as seen in Table 2 where Hewlett Packard Paper Acceptance Criteria software was used. Alternately, internal sizing of the sheet can be increased to give a similar advantage, or a combination of internal and Selvol PVOH surface sizing may be used. The addition of silica pigment to the formulation may decrease black print density in light coat-weight treated papers, but will significantly enhance other properties. Size press additives such as styrene malice anhydride (ammonium salt) can be used to minimize this decrease in black print density when incorporating silica pigments.
TABLE 1: Selvol Polyvinyl Alcohol Product Line
Lorem ipsum dolor sit amet, consectetur adipiscing elit. Ut elit tellus, luctus nec ullamcorper mattis, pulvinar dapibus leo.
STANDARD GRADES
Grade | Hydrolysis, % | Viscosity, cP1 | pH2 |
---|---|---|---|
Super Hydrolyzed | |||
PVOH 125 | 99.3+ | 28.0-32.0 | 5.5-7.5 |
PVOH 165 | 99.3+ | 62.0-72.0 | 5.5-7.5 |
Fully Hydrolyzed | |||
PVOH 103 | 98.0-98.8 | 3.5-4.5 | 5.0-7.0 |
PVOH 107 | 98.0-98.8 | 5.5-6.6 | 5.0-7.0 |
PVOH 310 | 98.0-98.8 | 9.0-11.0 | 5.0-7.0 |
PVOH 325 | 98.0-98.8 | 28.0-32.0 | 5.0-7.0 |
PVOH 350 | 98.0-98.8 | 62.0-72.0 | 5.0-7.0 |
Intermediate Hydrolyzed | |||
PVOH 418 | 91.0-93.0 | 14.5-19.5 | 4.5-7.0 |
PVOH 425 | 95.5-96.5 | 27.0-31.0 | 4.5-6.5 |
Partially Hydrolyzed | |||
PVOH 502 | 87.0-89.0 | 3.0-3.7 | 4.5-6.5 |
PVOH 203 | 87.0-89.0 | 3.5-4.5 | 4.5-6.5 |
PVOH 205 | 87.0-89.0 | 5.2-6.2 | 4.5-6.5 |
PVOH 513 | 87.0-89.0 | 13.0-15.0 | 4.5-6.5 |
PVOH 523 | 87.0-89.0 | 23.0-27.0 | 4.5-6.5 |
PVOH 540 | 87.0-89.0 | 45.0-55.0 | 4.5-6.5 |
1 4% aqueous solution, 20°C. | 2 4% aqueous solution pH. |
TABLE 2: Test Results
Optical Density | Optical Density | ||
---|---|---|---|
Treatment (coat wt. g/m2/side) | Hercules Sizing | Monochrome Black | Composite Black |
Base Sheet | 1 second | 0.94 | 0.65 |
Selvol 107 (1.2) | 5.5 | 1.04 | 0.81 |
Selvol 325 (2.7) | 57.0 | 1.30 | 1.01 |
Starch (1.9) | 2.0 | 0.98 | 0.74 |
COLOR OPTICAL DENSITY
Unlike black, the optical density of cyan, magenta and yellow is improved by the addition of structured silica to PVOH formulations, even on lightly surface-sized papers. Figure 2 illustrates the type of improvement which is possible for the cyan colorant.
DRY TIME
Because of its excellent sizing efficiency, Selvol PVOH surface sizing without silica pigment addition may increase ink dry time undesirably in the same manner as moderate to high level of internal sizing. Figure 3 shows how the use of 100 parts of silica decreases ink dry time for a Selvol 107 size press treated sheet based on dry time measurements as outlined in the Hewlett Packard Paper Acceptance Criteria manual
SYNERGY WITH OPTICAL BRIGHTENERS
Optical brighteners are often used in printing paper surface size formulations to brighten and whiten the paper surface. PVOH and optical brighteners work synergistically with each other, often providing an increase of 1.5 to 2.5 points in brightness over starch/optical brightener formulations.
STARTING SIZE PRESS FORMULATIONS
Selvol 107 fully hydrolyzed, low molecular weight PVOH is the recommended binder for high size press solids and relatively low silica loading levels. Selvol 325 fully hydrolyzed, medium molecular weight PVOH is recommended for lower size press solids and greater silica loading levels. The exact ratio of PVOH to silica will need to be tailored to each individual base sheet, depending on the level of internal sizing and machine size press constraints. For most typical size press applications, the starting formulation shown in Table 3 is recommended.
TABLE 3: Size Press Formulation
Ingredient | Dry Parts |
---|---|
Silica | 100 |
Selvol 107/325 PVOH | 50 - 200 |
Solids | 8% to 15% for Selvol 107 5% to 10% for Selvol 325 |
Coat Weights | 2 - 5 g/m2/side |
1. "The effect of SMA surface sizes on the paper end-use properties." TAPPI, George Batten, Jan. 1995. 2. J.M. Huber Technical Bulletin |
COATING APPLICATIONS
PVOH is the preferred binder for ink jet coatings utilizing silica pigments. PVOH provides excellent binding strength and improved ink jet print quality versus typical latex binders used in other pigmented coating applications. Formulations for Selvol PVOH and silica pigment will, however, create fairly viscous coatings at relatively low solids. The viscosity that is developed is dependent upon the desired coating solids, the pigment-to-binder ratio, and most importantly, the grade of Selvol PVOH chosen as a binder.
PVOH VS. LATEX BINDERS
Coatings using Selvol PVOH as a silica binder provide excellent color and monochrome black image quality due to the ability of PVOH to quickly absorb the water-based ink into the coating layer. By quickly absorbing the inks, wicking, mottling and bleeding can be minimized. Coating formulations utilizing typical latex binders with silica pigment produce ink jet print images that are mottled, low in ink density, and that have poor ink wicking control. These undesirable results may be due to the surfactants used to stabilize the latex particles, which interfere with the wetting of the ink jet inks. The poor results may also be due to the poor absorption of the inks into the coating layer. Selvol PVOH is a naturally hydrophilic solution polymer and therefore, when using this material, surfactants are not required.
Table 4 illustrates the print ink density of monochrome black, composite black and cyan on coated paper made with three types of latex binders in comparison with a PVOH binder. The photographs in Figure 4 also demonstrate the superior ink wicking control shown in coatings containing PVOH compared with those containing latex binders.


TABLE 4: Ink Jet Analysis of Coated Papers - 100 Parts Silica/30 Parts Binder
Base Sheet | Selvol 523 PVOH | Acrylic | Vinyl Acetate | SBR | |
---|---|---|---|---|---|
Solutions Solids | n/a | 11.56 | 12.85 | 12.52 | 17.11 |
Viscosity (cPs) | n/a | 112 | 310 | 215 | 267 |
Coat Weight (g/m2/side) | n/a | 6.64 | 8.64 | 7.09 | 8.01 |
Monochrome Black O.D. | 0.96 | 1.32 | 0.88 | 0.88 | 0.79 |
Composite Black O.D. | 0.64 | 0.92 | 0.62 | 0.61 | 0.74 |
Cyan O.D. | 1.07 | 1.44 | 1.26 | 1.25 | 1.10 |
Composite Black Dot Area (mm2) | 0.023 | 0.0094 | 0.0150 | 80.0159 | 0.0267 |
TABLE 5: Brookfield Viscosity* - 100 Parts Silica/40 Parts PVOH
PVOH Grade | Hydrolysis, % | Molecular Weight | 16% Solids | 13% Solids | 10% Solids |
---|---|---|---|---|---|
Selvol 125 | 99.3 | medium | 12,400 cPs (5) | 510 cPs (3) | 75 cPs (3) |
Selvol 325 | 98.4 | medium | 12,520 cPs (5 | 285 cPs (3) | 55 cPs (3) |
Selvol 425 | 96 | medium | 8,180 cPs (5) | 235 cPs (3) | 50 cPs (3) |
Selvol 523 | 88 | medium | 480 cPs (5) | 122 cPs (3) | 35 cPs (3) |
Selvol 107 | 98.4 | low | 4,120 (4) | 1,055 (3) | > 50 cPs (3) |
Selvol 103 | 98.4 | low | gel (4) | 1,895 cPs (3) | > 50 cPs (3) |
Selvol 205 | 88 | low | 6,140 cPs | 120 cPs (3) | > 50 cPs (3) |
BINDING POWER OF PVOH
Although low molecular weight, partially hydrolyzed grades of Selvol PVOH will permit greater coating solids, the silica pigment binding strength will decline in comparison with medium molecular weight grades. Therefore, a binder level of 40 to 50 parts per 100 parts silica pigment will be required for the lower molecular weight grades in order to prevent dusting of the silica from the sheet surface. Medium molecular weight grades of Selvol PVOH will permit a binder-to-silica pigment ratio of 30 to 40 parts to 100 parts respectively. Actual binder-to-pigment ratios will have to be tailored for a given base sheet, coating method and silica surface area. Table 6 illustrates dusting potential as measured by rubbing black felt over coated sheets of various parts and grades of PVOH per 100 parts silica (ppt. amorphous @ 260 m2/gram surface area) on a slack-sized base sheet.
VISCOSITY/RHEOLOGY VS. SOLIDS
Due to hydrogen bonding between the PVOH hydroxyl groups and the silanol groups on the silica pigment, the final viscosity of PVOH/silica coatings increases sharply with small increases in solids. This phenomenon maximizes solids at 25% to 30%, depending on the grade of PVOH and the pigment-to-binder ratio. Higher hydrolysis grades (greater percent of OH groups) of PVOH tend to produce greater viscosity at a constant pigment-to-bonder ratio. Medium molecular weight Selvol grades generally produce greater viscosity than lower molecular weight grades. hydrogen bonding between the PVOH hydroxyl groups and the silanol groups on the silica pigment, the final viscosity of PVOH/silica coatings increases sharply with small increases in solids. This phenomenon maximizes solids at 25% to 30%, depending on the grade of PVOH and the pigment-to-binder ratio. Higher hydrolysis grades (greater percent of OH groups) of PVOH tend to produce greater viscosity at a constant pigment-to-bonder ratio. Medium molecular weight Selvol grades generally produce greater viscosity than lower molecular weight grades.
Typically, partially hydrolyzed low/medium molecular weight grades allow for the highest level of coating solids. Pigment- to-binder ratios that are high in PVOH binder will also result in greater viscosity within a given solids level and PVOH grade. Incorporation of pigments other than silica could reduce the overall coating viscosity and thus allow for a greater coating solids level versus an all-silica pigment coating.
Table 5 illustrates the Brookfield viscosity of a 100 parts silica/400 parts PVOH coating made with various grades of Selvol PVOH at various coating solids.
High shear rheology of PVOH/silica coatings is also dependent on the polymer’s degree of hydrolysis and molecular weight
as well as the coating solids and pigment-to-binder ratio. Modification of the silica pigment, such as fumed silica containing a small percent of AI2O3, will also reduce shear thickening effects of the coating. The graphs in Figures 4 and 5 illustrate the high shear rheology of a 100 parts silica/40 parts PVOH coating at 13% solids using various grades of Selvol. The coatings were measured on ACAV high shear capillary rheometer capable of measuring viscosity and shear stress responses at shear rates of up to 3 million reciprocal seconds.
ADDITIVES
Selvol PVOH possesses a nonionic charge and, therefore, is compatible with most coating additives, including all types of cationic additives and surface sizing agents. To help improve the water-fastness and to reduce ink bleeding of the ink jet printed sheet, cationic dye fixatives are recommended as part of the coating formulation. Cationic polymers such as polyethyleneimine, poly-DADMAC or polyvinyl amine at addition levels of 1 to 3 parts by weight, should provide the desired characteristics.
RECOMMENDED GRADES AND STARTING FORMULATIONS
Selvol 523, Selvol 205 or Selvol 203 are the recommended PVOH grades for coating applications. They are partially hydrolyzed (87-89% ) with medium, low and ultralow molecular weights respectively. Formulations containing these products will allow for maximum coating solids and lower high-shear rheology, as compared with their fully hydrolyzed counterparts. Recommended starting formulations for ink jet coatings are shown in Tables 7 and 8.
COATING FORMULATION MAKEDOWN
The following procedure is suggested for the preparation of a silica/Selvol coating:
- Slurry the silica pigment at the highest possible solids according to the manufacturer’s
- Solubilize the Selvol PVOH by the slowly slurrying the solid powder into <90˚F water and raising the temperature to 205˚F. Hold the temperature at this level for 20 to 30 The addition of a defoamer prior to solubilization of the PVOH is recommended.
- Slowly add the silica slurry to the solubilized PVOH under agitation after the temperature of the PVOH solution has dropped below 130˚F.
Mix in additives after the PVOH has been added
TABLE 6: Dusting Potential - 100 Parts Silica/Various Parts PVOH
PVOH Grade | 30 Parts PVOH | 40 Parts PVOH | 50 Parts PVOH |
---|---|---|---|
Selvol 125 | Slight | No Dusting | No Dusting |
Selvol 325 | Slight | No Dusting | No Dusting |
Selvol 425 | Slight | No Dusting | No Dusting |
Selvol 523 | Slight | No Dusting | No Dusting |
Selvol 107/103 | Moderate to Heavy | Slight to Moderate | No Dusting |
Selvol 205/203 | Moderate to Heavy | Slight to Moderate | No Dusting |
TABLE 7: Air Knife Coating Formulation
Ingredient | Dry Parts |
---|---|
Silica | 100 |
Selvol 523 PVOH | 30 - 40 |
Defoamer* | 0.05 - 0.1 |
Cationic Additive | 1 |
Solids | 15% to 18% |
Viscosity | 200 - 600 cPs |
Coat Weight | 8 - 12 g/m2/side |
*Foammaster VF from Henkel Corp. and Antifoam 116FG from Harcross Chemical are recommended defoamers. |
TABLE 8: Rod/Blade Coating Formulation
Ingredient | Dry Parts |
---|---|
Silica | 100 |
Selvol 203/205 PVOH | 40-50 |
Defoamer* | 0.05 - 0.1 |
Cationic Additive | 1 |
Solids | 15% to 30% |
Viscosity | 200 - 6000 cPsv |
Coat Weight | 8 - 12 g/m2/side |
*Foammaster VF from Henkel Corp. and Antifoam 116FG from Harcross Chemical are recommended defoamers. |